
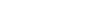
-
Quality
-
Partners
-
News
-
Responsibility
-
About Us

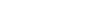
-
Quality
-
Partners
-
News
-
Responsibility
-
About Us


-
Home
-
About US
- About US
- Responsibility
- News
- Partners
-
Solutions
-
Products
-
Support
- Service
- Quality
-
Contact Us


-
Home
-
About US
- About US
- Responsibility
- News
- Partners
-
Solutions
-
Products
-
Support
- Service
- Quality
-
Contact Us
Delivering greater effluent and productivity, while reducing lifecycle cost with MBR technology
For more than tow decades, WEBSTER® has led the membrane industry. Since 1999, we have dedicated a team strictly to Membrane Bioreactor (MBR). Today, our technology operates in more than 200 municipal and industrial plants across the globe.
Proven to deliver greater effluent and productivity, while reducing the lifecycle cost, MBR technology is preferred by the market. Our technology uses a fully automated process that provides liquid/solid separation by combining biological waste oxidation and membrane separation. In turn, this eliminates the need for any secondary clarification or tertiary filtration.
The WEBSTER® MBR system delivers greater stability of the membrane environment, operational flexibility, and reduced maintenance requirements, resulting in significant cost savings. The system is successfully operating in applications ranging from municipal wastewater plants to the most difficult industrial applications such as oil refineries and landfill leachate.
We're here to help.
If you'd like to talk with a sales representative about purchasing WEBSTER's products and services, you can reach us here.
Proven durability and low maintenance with MBR
Aeration Like No Other
● The unique efficiency of two-phase plug flow WEBSTER® membrane cleaning.
● No need for daily cyclic peak operation.
● Doesn’t waste energy – 1: 1 focused bubble.
● Low chemical use.
In Tank: Membranes Where They Belong
● Keeps your team productive with no need to adjust slack.
● Fully automated membrane cleaning.
● Minimize operator exposure to bacteria & pathogens.
Filtration Strong Durability
● Strength where you need it: 100% UF membrane.
● Can withstand force in all directions.
● Self-healing smaller ID membranes.
● Reliable effluent quality with proven pathogen rejection for > 10 yrs.
● Enabling re-use – Tier 3 capable.
Adaptable and Flexible
● State-of-the art modular and configurable rack design.
● Can fit into any tank geometry.
● Fits into other membrane system cassette and rack layouts.
● Compact MBR footprint: approximately 30% smaller.
MBR systems are for the treatment or reuse of a variety of wastewaters
Today, most MBR applications are for the treatment or reuse of municipal wastewaters. MBR systems may be applied to a variety of wastewaters from the cosmetics, pharmaceuticals, textile, food and beverage, pulp and paper, and chemical industries, as well as blackwater, greywater, and landfill leachate.
MBR systems combine a biological process and a low-pressure membrane filtration process, so expert knowledge in both areas is essential. The biological portion of an MBR is largely similar to activated sludge process commonly used in treating municipal and industrial wastewaters. With the design primarily for removing dissolved and suspended organic matter from the wastewater, the method requires that an assortment of microorganisms be present in the same reactor.
A major consideration in selecting membranes for MBRs is the need to minimize fouling. This is dependent on feedwater quality and aspects of the system design such as: membrane material, module dimensions, flux, and conditions at the membrane interface. Advanced fouling control today typically uses random large bubble air scouring combined with mixed liquor pumping to provide a low energy, low fouling MBR system.